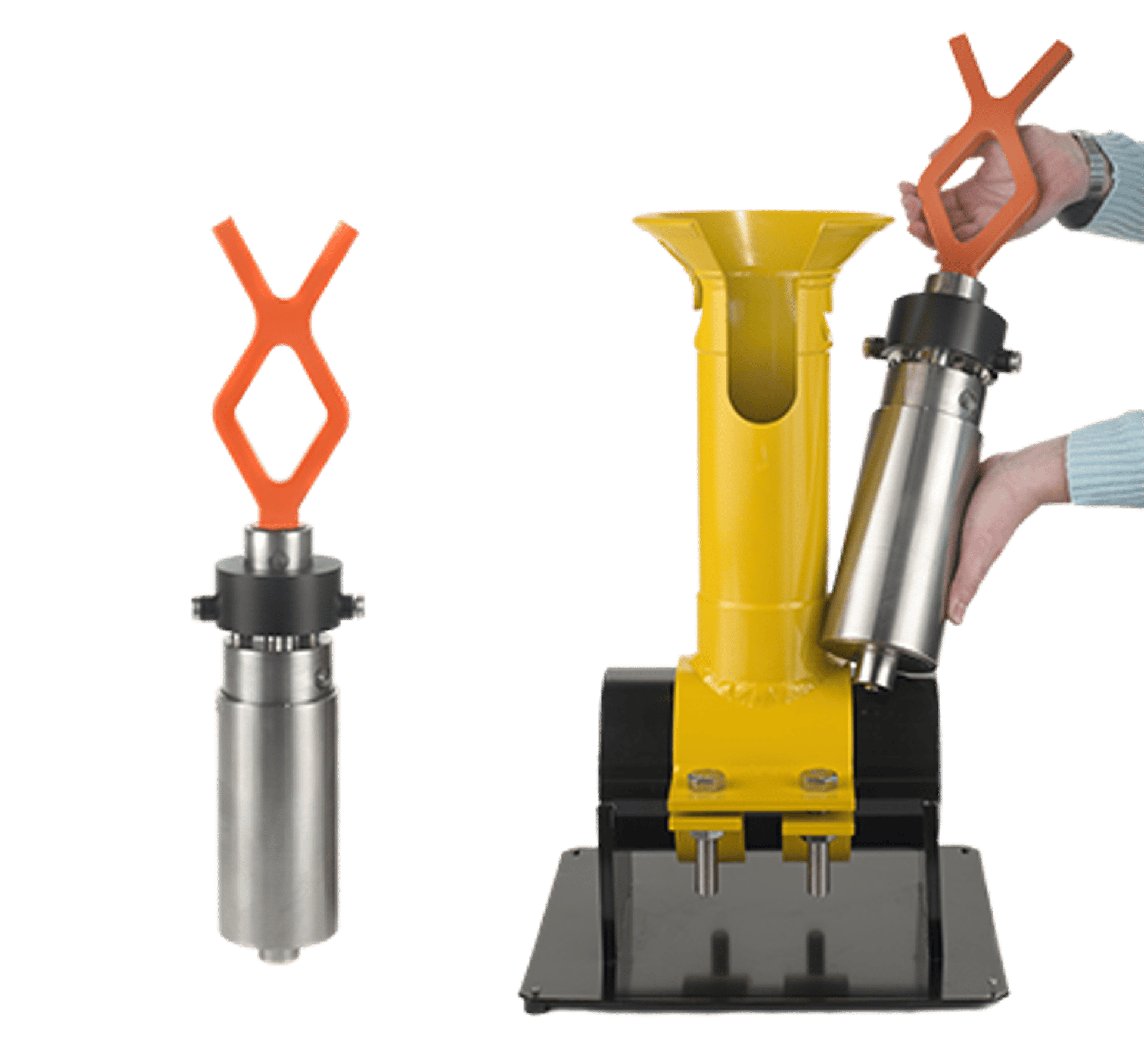
SUBSEA LEAK MONITOR
The Non-intrusive ClampOn DSP Leak Monitor detects small and medium leaks or flow-throughs, even with low differential pressure over the measuring point on pipes and valves. The ClampOn DSP Leak Monitor has been developed with the aim of offering a product that can quantify a leak through a closed valve. The ClampOn DSP Leak Monitor is qualified as a subsea and topside monitor.
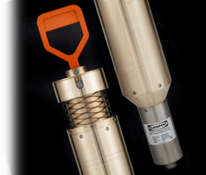
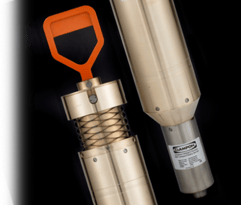
SUBSEA LEAK MONITOR
HOW IT WORKS
The basic theory is that a leak creates a very high-frequency noise that can be monitored by an ultrasonic sensor. In a «non-leak» situation the ultrasonic pattern will be stable, but when a leak occurs the signature will change drastically. ClampOn’s DSP technology distinguishes and eliminates background noise unrelated to leakages so that the hiss from the leaks can warn the operator. The system also includes a program or data-base that helps to monitor and indicate the volume of the leak.
The ClampOn DSP Leak Monitor is the result of a joint venture project involving several participants in the petroleum industry.
The ClampOn DSP Leak Monitor is designed to be installed at critical points such as valves, flanges, joints, etc., and can monitor very small leakages. A pressure differential of as little as 1 bar can be monitored in gases, and 3 bar in liquids.
The ClampOn subsea sensors are designed to meet these requirements:
Designed for a service life of more than 25 years
Independent redundant electronics
Independent high and atmosphere pressure chambers
Electron beam (EB) welding of the chamber against external pressure (no rubber or mechanical seals)
Glass-metal penetrator as a barrier between high and atmosphere pressure chambers
Outstanding sensitivity, repeatability, accuracy and signal/noise ratio thanks to Digital Signal Processing (DSP)
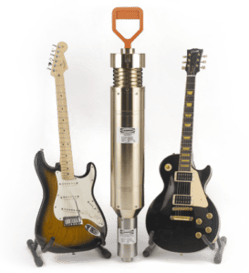
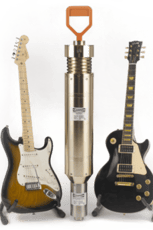
ADVANTAGES
A leak in an oil or gas flow line is a highly dangerous situation – upstream as well as downstream, so it is extremely important for the operator to be warned about any leak immediately should it occur.
A leak in a flow line, valve, flange or any other component can compromise safety and may also lead to a shutdown at the production stage or down-stream at a refinery or terminal.
A product leak normally has a very low flow-rate, which is determined by the size of the defect, the properties of the fluid and the pressure differential. There are a number of advantages in using the DSP Leak Monitor to monitor valves:
Reduced loss to flare
Gas leak to the sea
Reduced loss to the atmosphere
Reduced process loss
Maintenance planning
The ClampOn DSP Leak Monitor helps operators identify and quantify sources of gas/liquid leakages, thus enabling them to take appropriate action. Customers have successfully used the ClampOn Leak Monitor to identify cross-flow in valves connected to the manifold.
INTEGRATION
Our instruments can easily be integrated into any existing or new control system. A computer with our software is often used in-between our instruments and the control system. The computer will be used for calculations and all recorded data will be stored for analyzing and calibration purposes.
We always recommend using the digital interface due to following benefits:
Two way communication enabling instrument software update and configuration
Full signal range resolution
All sensor data can be transmitted
No signal loss
SUBSEA LEAK MONITOR
Principle of operation
Passive acoustics, intelligent sensor
Minimum minimum leakage
Gas: dP>1 bar, min. leakage rate 0.1 l/min
Liquid: dP>3 bar, min. leakage rate 0.1 l/min
(depending on delta pressure [dP] over the leakage point)
Repeatability
1%
Method of installation
Clamped to pipe surface, non-intrusive
Sensor electronics
Intelligent DSP electronics with signal processing
Interface options
All sensors can be supplied with:
Digital RS485 (ASCII, binary, ModBus RTU), 4-20mA (active/passive). Relay (Other options on request).
Options: CANBus, Profibus
Two-way communication
Yes
Software upgrading
Yes
Pipe Surface Temperature
-40 °C to +225 °C (-40 °F to +437 °F)
High temperature fixture
Yes – up to 500 °C (932 °F)
Flow regimes
Intelligent health-test of electronic hardware
COMPUTER
Minimum hardware
Pentium III (or equivalent) with 512 MB RAM
Software requirements (for ClampOn Software)
Windows 2000/2003/XP/Vista
Signal interface to Client system (typical)
RS232 / RS485 / Relay / ModBus / TCP I/P – Optional 4-20mA / Relay
SPECIFICATIONS
ADDITIONAL INFORMATION
COMPACT MODEL
Water depth
3000m
Max. operating pressure barA
300 (4351psi)
Max. test pressure barA
333 (4829psi)
Housing material
Titanium
Dimensions excl.ROV handle
ø90 x 324mm (ø3.5” x 12.8”)
Dry weight, kg (lbs)
5.2 (11.5)
Hose/jumper interface
Bennex or ODI
Independent redundant electronics / single electronic
Yes
Gasket / sealing
No
EB welding
Yes
Glass-metal penetrator
Low pressure / high pressure chamber
Yes
ROV installation / retrieval
Yes
Retrofit clamp / funnel
Yes
Power Supply
12-28VDC
Current draw
Approx. 70mA @ 24VDC
Design Lifetime (MTBF)
220 000 hours (25 years)
Quality, not quantity
Get in touch
Address
Head Office:
Jl. CBD Gading Serpong Blok F/12 Ruko Pasar Modern Paramount,
Tangerang Banten - 15810
Branch Office:
Perumahan Pondok Karya Agung Jl. Kasuari Blok TA No 25
Kelurahan Sungai Nangka, Balikpapan Selatan, Balikpapan - 76114
Contacts
021-29324571
021-29324572
info@ptaii.co.id