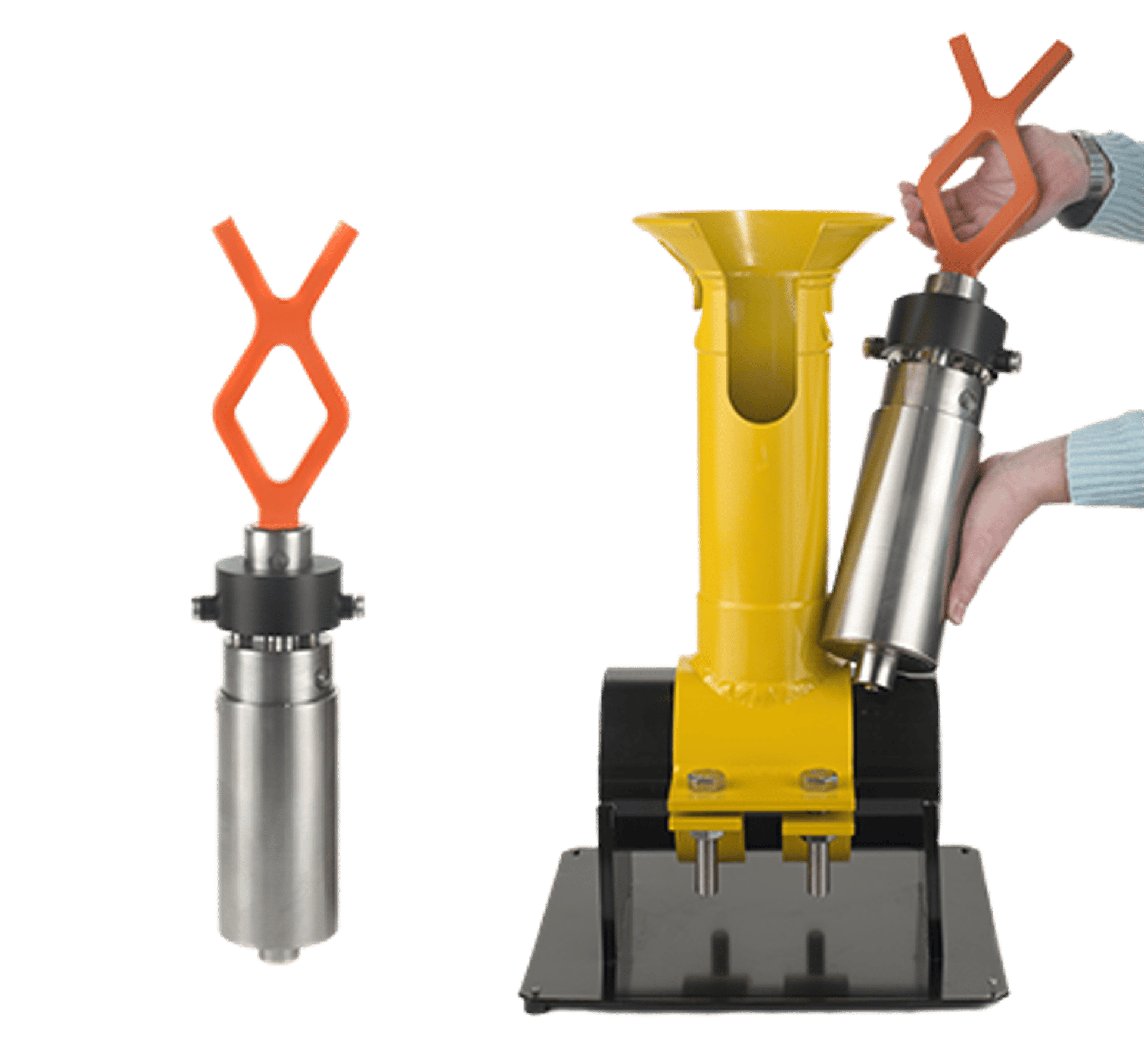
CLAMPON CORROSION-EROSION MONITOR
The ClampOn Subsea Corrosion-Erosion Monitor (CEM) continually monitors and quantifies changes in wall thickness over a large area of a pipeline. The non-intrusive instrument estimates the rate at which corrosion and/or erosion reduces the thickness of the pipe wall. In this way, it can provide operators with an early warning of potentially catastrophic failures before they occur. The CEM is therefore also an effective tool in helping operators comply with newer regulations regarding the need for condition monitoring. It can be retrofitted to existing structures or installed on new pipelines before they are deployed subsea.
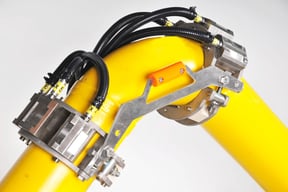
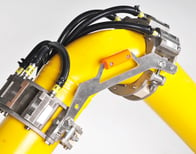
SUBSEA CORROSION-EROSION MONITOR
HOW THE SUBSEA CORROSION-EROSION MONITOR WORKS
The ClampOn Subsea Corrosion-Erosion Monitor measures and monitors wall thickness loss in pipes, plates or other metal structures. The non intrusive sensors uses Acoustic Guided Lamb Waves (AGLW), a technology that gives an average wall thickness reading for a large section of pipe. Transducer pairs operate in a pitch-catch mode and use the ultrasonic waves to give the average wall thickness between the transducer pairs. The transducers are fixed at pre-determined points on the pipe to monitor the wall thickness loss in sections of the pipe typically up to two meters long.
The Corrosion Monitor/Erosion Monitor unit can consist of 2 – 32 transducers and an electronics unit that handles all signal acquisition and processing. The non-intrusive subsea Corrosion-Erosion Monitor can utilize up to 32 transducers, increasing distance to a maximum of 8 meters. Wall thickness trends are generated automatically and can be observed in real-time on a computer running ClampOn CEM software, or logged internally in a data logger.
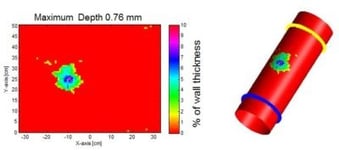
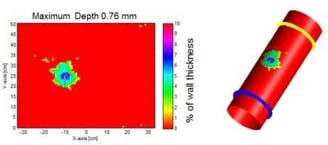
System properties (CGV mode)
The system measures the wall thickness loss between pairs of transducers
The system will have between two and thirtytwo transducers in operation
The sensitivity for wall thickness assessment is around 0,1% of wall thickness (WT) over the full temperature range
Can detect changes as small as 0,1% of wall thickness
The system measures wall thickness in REAL time, at user-definable intervals
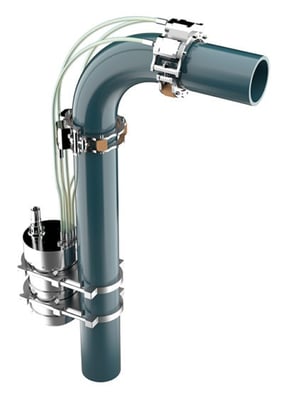
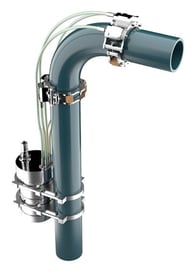
Wall thickness map (left) obtained on a pipe with two circular arrays of transducers (right). Actual wall thickness 0.76 mm, pipe OD 8.625 in.
ADVANTAGES
There are three different models available for the ClampOn Subsea Corrosion-Erosion Monitor, all non-intrusive, one ROV-installable for existing pipes and structures, and one pre-installable solution that can be installed topside before the structure is submerged and one model that can be installed by diver. All models operate in the same way and will give the same results when it comes to reliability and repeatability.
Read Audun O. Pedersen’s (ClampOn) article in Oilfield Technology, January 2017:
– Combatting Corrosion »
Transducers are clamped to the outside of the pipe using active ultrasound and exploiting the properties of Acoustic Guided Lamb Waves to detect the changes in wall thickness relative to reference values obtained during the installation of the system. The monitor is designed for permanent installation and will not need any calibration after installation. A variety of configurations are possible. It can act as a standalone monitor running on batteries that have a lifetime of 10 years and sending the data acoustically to the surface, or it can be integrated into the control system via existing cables.
Many governments and petroleum regulations require permanent monitoring of a pipe’s condition, and this instrument provides a constant stream of information about the pipe’s condition at critical points. By installing the Corrosion Monitor/Erosion Monitor the operator can constantly monitor any changes in wall thickness, and will know when if necessary to replace sections of pipe or if there is a risk of leakage.
INTEGRATION
The Corrosion-Erosion Monitor can be interfaced using Ethernet, RS-485/422/232, acoustic modems or indirectly using battery packs with internal logging and a USB interface.
The instrument has a dual Ethernet interface built in, and supports Modbus TCP/IP, OPC UA, FTP, HTTP, NTP and numerous other IP-based industry standard protocols. As a member of SIIS, the Subsea Instrumentation Interface Standards JIP, ClampOn participated in developing the standard for Ethernet-based instrument interfaces subsea (SIIS Level 3). The CEM passed all the SIIS Level 3 tests at the SIIS plugfest in April 2016.
In case Ethernet is not available on the control system side, the subsea Corrosion-Erosion Monitor also has serial interfaces (RS-485 and RS-232) which support Modbus RTU. Whether the Ethernet or direct serial interfaces are used, the instrument can be managed via a transparent link using the CEM Client application, which supports rich functionality (software updates, historical trending etc.) using user defined Modbus function codes.
On locations without wired communication and/or power, the CEM can hand off results via an acoustic link, or store the results in a retrievable battery pack. The acoustic link or battery pack can also communicate configuration updates to the subsea instrument.
SPECIFICATIONS
Subsea Corrosion-Erosion Monitor
Method of operation:
Active ultrasound w/EMAT transducers
Coverage area:
Typical 3 m² (32 ft²) **
Changes:
0.1 %
Repeatability:
Better than 1 %
Wall thickness range:
8 mm to 50 mm (0.314" to 1.968")
Minimum pipe OD:
4 Inch NPS (114 mm)
Wall material:
Conductive metals and alloys
Design life:
30 Years (10+ Years for ROV mounted system)
Electronics:
8/16 channel CEMAT with automation controller*
Communication:
SIIS L2, SIIS L3 (Modbus TCP/IP) or Serial RS485 (Modbus RTU)
Power supply:
18-32 VDC, Battery *
Design depth:
3050 m (10.000 ft)
* Examples shown. System is tailored for integration
** Limitations depend upon pipe geometry and configuration
All specifications are subject to change without notice
DATASHEET

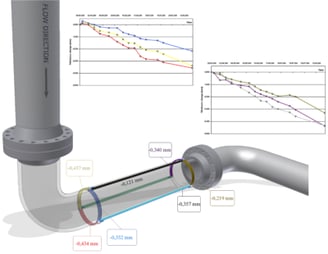
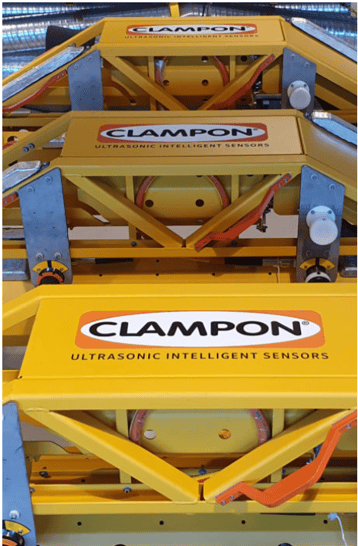
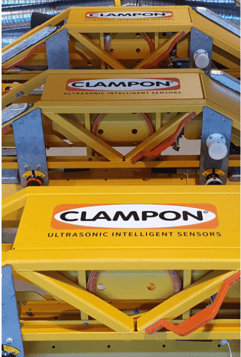
ADDITIONAL INFORMATION
Quality, not quantity
Get in touch
Address
Head Office:
Jl. CBD Gading Serpong Blok F/12 Ruko Pasar Modern Paramount,
Tangerang Banten - 15810
Branch Office:
Perumahan Pondok Karya Agung Jl. Kasuari Blok TA No 25
Kelurahan Sungai Nangka, Balikpapan Selatan, Balikpapan - 76114
Contacts
021-29324571
021-29324572
info@ptaii.co.id